List of Measuring Tools Used in Machine Shop: Ensuring Precision and Accuracy
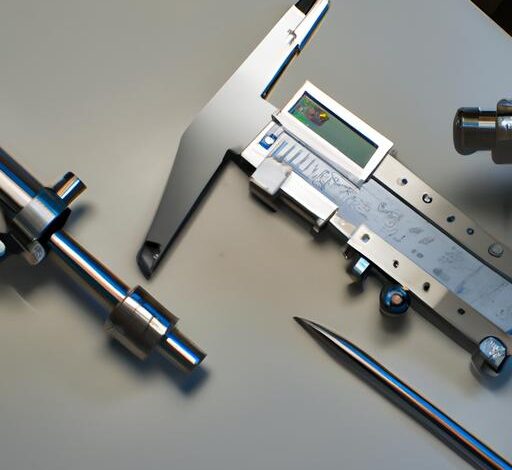
In the world of machine shops, precision is paramount. Every component, every part, every product must be crafted with meticulous accuracy to ensure optimal performance. And at the heart of this precision lies a crucial arsenal of measuring tools. These tools are the unsung heroes, the silent champions that enable machinists to bring their creations to life with unwavering accuracy.
Introduction
When it comes to machine shops, the importance of measuring tools cannot be overstated. These tools serve as the guiding compass, ensuring that every cut, every drill, and every turn of the wrench aligns perfectly with the desired specifications. They are the reliable companions that transform mere metal into finely tuned machinery.
But why are these measuring tools so crucial? Well, imagine a world without them. A world where we rely on guesswork and estimations. Would you trust a surgeon who eyeballs the length of an incision or a chef who measures ingredients with a vague sense of approximation? Of course not. Precision requires precision tools, and in the realm of machine shops, the stakes are equally high.
Using the right measuring tools is crucial for achieving precise results. These tools provide the ability to measure dimensions, angles, depths, and tolerances with incredible accuracy. From the simplest calipers to the most sophisticated coordinate measuring machines (CMMs), each tool in the machine shop arsenal plays a vital role in ensuring that the finished product meets the highest standards of quality.
So, in this comprehensive article, let’s delve into the world of measuring tools used in machine shops. We will explore the various types, their applications, and the advantages they bring to the table. Whether you are a seasoned machinist or just starting your journey in the world of machine shops, this list of measuring tools will serve as your trusted guide, enabling you to navigate the intricacies of precision with confidence.
Now, let’s embark on this exciting journey together and uncover the vast array of measuring tools that make machine shops the epitome of precision engineering.
Basic Measuring Tools
A. Definition and Description of Basic Measuring Tools
In the realm of machine shops, basic measuring tools are the foundation upon which precision is built. These tools, though simple in design, possess the remarkable ability to accurately measure dimensions, ensuring that every cut and adjustment aligns with exact specifications.
Calipers, one of the most common basic measuring tools, come in various forms, such as vernier calipers and dial calipers. These devices consist of two arms with jaws at the end that can be adjusted to measure both internal and external dimensions. Calipers provide precise readings, often to the nearest hundredth of a millimeter, making them indispensable for machinists seeking accuracy.
Another essential tool in this category is the micrometer. This handheld device allows for incredibly precise measurements, typically to the nearest thousandth of an inch or tenth of a millimeter. Micrometers utilize a calibrated screw mechanism to measure the dimensions of cylindrical objects, providing machinists with unparalleled accuracy.
B. Importance of Basic Measuring Tools in Machine Shops
Basic measuring tools may be humble in appearance, but they play a critical role in ensuring the quality and precision of machined components. Without these tools, machinists would be left to rely on estimations and guesswork, compromising the integrity and performance of their creations.
By utilizing basic measuring tools, machinists can verify the accuracy of their work at every step of the process. Whether it’s measuring the diameter of a hole, the thickness of a metal plate, or the length of a shaft, these tools provide the means to achieve the desired dimensions with confidence. They serve as the machinist’s trusted companions, enabling them to transform raw materials into perfectly crafted components.
C. Examples and Uses of Basic Measuring Tools
Basic measuring tools find application in a wide range of tasks within the machine shop. Calipers, with their versatility, are ideal for measuring external dimensions of objects, such as the thickness of a sheet metal or the diameter of a rod. They can also be used to measure internal dimensions, like the diameter of a hole or the width of a groove.
Micrometers, on the other hand, excel at measuring precise dimensions of cylindrical objects. Whether it’s measuring the diameter of a shaft, the thickness of a precision washer, or the depth of a groove, micrometers provide the accuracy required for these critical measurements.
In addition to calipers and micrometers, other basic measuring tools include rulers, depth gauges, and feeler gauges. Each of these tools serves a specific purpose, allowing machinists to measure lengths, depths, and clearances with confidence and precision.
By embracing and mastering the use of these basic measuring tools, machinists lay the foundation for excellence in their craft. These tools empower them to achieve the highest standards of accuracy, ensuring that every component they produce meets the exacting demands of the industry.
Precision Measuring Tools
Definition and Description of Precision Measuring Tools
Precision measuring tools are the masters of accuracy in the realm of machine shops. These tools elevate the level of precision to new heights, allowing machinists to achieve measurements with utmost accuracy and reliability. Among the arsenal of precision measuring tools are height gauges and dial indicators.
Height Gauges: A height gauge is a versatile tool used to measure the vertical distance between two points. It typically consists of a base, a vertical column, and a measuring arm. Machinists rely on height gauges to determine the height of workpieces, measure depths, and ensure the parallelism of surfaces. With its precise scale and adjustable arm, this tool enables machinists to achieve consistent and accurate measurements.
Dial Indicators: Dial indicators, also known as dial gauges or dial test indicators, are compact devices designed to measure small linear distances with exceptional precision. These tools consist of a needle-like pointer attached to a dial face, which provides readings in increments as small as 0.001 inches or 0.01 millimeters. Machinists utilize dial indicators to measure deviations, alignments, and runout in machine components, ensuring that everything is perfectly aligned for optimal performance.
Significance of Precision Measuring Tools for Accurate Measurements in Machine Shops
In the world of machine shops, precision is the name of the game. Whether it’s manufacturing intricate components or ensuring the seamless assembly of complex machinery, accurate measurements are crucial. This is where precision measuring tools shine. They offer machinists the ability to measure with incredible accuracy, helping them achieve the desired specifications and tolerances.
Precision measuring tools play a pivotal role in quality control processes, ensuring that every part meets the stringent requirements for performance and functionality. By utilizing height gauges and dial indicators, machinists can identify even the slightest deviations, enabling them to make precise adjustments and corrections. These tools empower machinists to deliver products that surpass expectations and withstand the test of time.
Detailed Explanation and Applications of Precision Measuring Tools
Height gauges and dial indicators find applications in a wide range of machining tasks. Machinists rely on height gauges to measure the height of workpieces accurately, ensuring that they meet the required dimensions. Additionally, height gauges are instrumental in checking the parallelism of surfaces, crucial for maintaining the precision of machine components.
Dial indicators, on the other hand, are invaluable when it comes to detecting deviations and misalignments. Whether it’s checking for runout in rotating parts or verifying the concentricity of cylindrical components, dial indicators provide the precision necessary for fine adjustments. They enable machinists to identify and rectify imperfections, ensuring optimal performance and smooth operation.
In conclusion, precision measuring tools such as height gauges and dial indicators are indispensable companions in the realm of machine shops. Their ability to provide accurate measurements and detect deviations with exceptional precision ensures that every product meets the highest standards of quality. With these tools in hand, machinists can confidently navigate the intricacies of precision machining, delivering results that exceed expectations.
Specialized Measuring Tools
Introduction to Specialized Measuring Tools Used in Machine Shops
In the intricate world of machine shops, where precision reigns supreme, specialized measuring tools take center stage. These tools are designed to tackle specific challenges and provide machinists with the utmost accuracy in their measurements. Let’s dive into the realm of specialized measuring tools and explore how they elevate the precision game in machine shops.
Explanation of the Purpose and Benefits of Specialized Measuring Tools
Specialized measuring tools serve a specific purpose, honing in on particular aspects of measurement that demand meticulous attention. Unlike their basic counterparts, these tools are tailored to meet the unique requirements of specific tasks, ensuring the highest level of precision and accuracy.
The benefits of specialized measuring tools are manifold. By focusing on specific measurements, these tools enable machinists to achieve unparalleled accuracy in critical areas. They allow for precise evaluation of complex features, intricate geometries, and hard-to-reach dimensions. With specialized tools in hand, machinists can confidently tackle intricate projects, knowing that they have the means to measure with utmost precision.
Examples and Uses of Specialized Measuring Tools
There is a wide range of specialized measuring tools utilized in machine shops, each with its own distinct purpose and application. Let’s explore a couple of examples that showcase the versatility and significance of these tools:
Bore Gauges
Bore gauges are indispensable for measuring the internal diameter of cylindrical holes. These tools come in various forms, including telescopic, dial, and snap gauges, each suited to specific measurement requirements. Bore gauges allow machinists to ensure that bores meet the desired specifications, guaranteeing proper fit and alignment of components.
Thread Gauges
Thread gauges are essential for measuring the pitch, diameter, and profile of threaded fasteners. These tools come in handy when verifying the accuracy of threaded holes, bolts, and screws. With thread gauges, machinists can ensure that threads are precisely machined, promoting smooth assembly and secure connections.
These examples merely scratch the surface of the myriad specialized measuring tools used in machine shops. From gear tooth micrometers to surface roughness testers, each tool serves a specific purpose, elevating the precision and quality of the machinist’s craft.
With specialized measuring tools in their arsenal, machinists can conquer the most intricate measurements, ensuring that every aspect of their creations meets the highest standards of excellence. So, embrace the power of specialization and equip yourself with the tools that enable precision engineering in the world of machine shops.
Advanced Measuring Tools
In the ever-evolving landscape of machine shops, technology has paved the way for advanced measuring tools that take precision to new heights. These cutting-edge instruments combine innovation with accuracy, allowing machinists to push the boundaries of what is possible. Let’s explore some of these advanced measuring tools and understand their significance in modern machine shops.
A. Definition and Description of Advanced Measuring Tools
Coordinate Measuring Machines (CMMs)
At the forefront of advanced measuring tools stands the remarkable Coordinate Measuring Machine (CMM). This sophisticated device utilizes a combination of precision sensors, probes, and computer software to measure intricate geometries with unparalleled accuracy. Offering three-dimensional measurement capabilities, CMMs enable machinists to inspect and verify complex components, ensuring adherence to stringent tolerances. From automotive parts to aerospace components, CMMs play a pivotal role in guaranteeing the quality and precision of the finished product.
Optical Comparators
Another invaluable tool in the arsenal of advanced measuring instruments is the Optical Comparator. Utilizing the principles of optics, these machines project magnified images of a part onto a screen, allowing machinists to compare it against a reference template. Optical comparators enable quick and accurate measurements of dimensions, angles, and profiles, making them indispensable in industries where speed and precision are paramount. With their ability to enhance visualization and simplify complex measurements, optical comparators streamline the inspection process and provide machinists with valuable insights.
B. Importance of Advanced Measuring Tools in Modern Machine Shops
In today’s fast-paced manufacturing environment, time is of the essence. Modern machine shops must strive for efficiency without compromising on quality. Advanced measuring tools play a pivotal role in achieving this delicate balance. By automating complex measurement processes and reducing human error, these tools significantly enhance productivity while maintaining the highest standards of accuracy. As technology continues to advance, the integration of advanced measuring tools becomes increasingly crucial for remaining competitive in the industry.
C. Detailed Explanation of Advanced Measuring Tools and Their Applications
The applications of advanced measuring tools are vast and diverse. Coordinate Measuring Machines (CMMs) find extensive use in industries such as automotive, aerospace, and medical, where precision is paramount. From inspecting critical engine components to validating intricate surgical implants, CMMs ensure that every measurement meets exact specifications. Optical comparators, on the other hand, find their niche in industries like manufacturing, tool and die, and electronics, where rapid inspection of intricate parts is essential. These tools enable machinists to verify dimensions, check for defects, and ensure the overall quality of the manufactured components.
In conclusion, advanced measuring tools are the epitome of technological innovation in the realm of machine shops. Coordinate Measuring Machines (CMMs) and Optical Comparators empower machinists to achieve unparalleled levels of precision, streamline inspection processes, and meet the stringent demands of modern manufacturing. By embracing these advanced measuring tools, machine shops can elevate their capabilities, enhance productivity, and deliver products of exceptional quality.
Conclusion
In the realm of machine shops, precision and accuracy reign supreme, and it is the measuring tools that serve as the backbone of this precise craftsmanship. From the basic calipers and micrometers to the advanced coordinate measuring machines (CMMs) and optical comparators, each tool has its place in ensuring that every component meets the desired specifications.
Throughout this article, we have explored the importance of using the right measuring tools in machine shops. These tools allow machinists to achieve unparalleled precision, resulting in products that not only meet but exceed expectations. The ability to measure dimensions, angles, depths, and tolerances with utmost accuracy is what sets machine shops apart as bastions of quality engineering.
As we conclude our exploration of the list of measuring tools used in machine shops, it is essential to recognize the significant impact these tools have on the final product. They enable machinists to transform raw materials into finely crafted machinery, knowing that every measurement has been meticulously taken and every cut has been executed with precision.
So, whether you are a seasoned machinist or a novice venturing into the world of machine shops, it is crucial to familiarize yourself with the wide range of measuring tools available. Embrace the calipers, micrometers, height gauges, dial indicators, and all the specialized tools that enhance your ability to create with accuracy.
Remember, precision is not just a goal; it is a mindset. By using the right measuring tools, you can elevate your craft, surpass expectations, and build a reputation as a master of precision engineering.
So, equip yourself with the knowledge, embrace the tools, and embark on a journey of precision and excellence in the captivating world of machine shops. Let the measuring tools be your trusted companions, guiding you towards the pinnacle of craftsmanship.
Now, go forth and measure with confidence, for the world of machine shops awaits your precision touch!
Conclusion: So above is the List of Measuring Tools Used in Machine Shop: Ensuring Precision and Accuracy article. Hopefully with this article you can help you in life, always follow and read our good articles on the website: cook.mahjong-gratuit.net