What is the Difference Between MIG and TIG Welders?
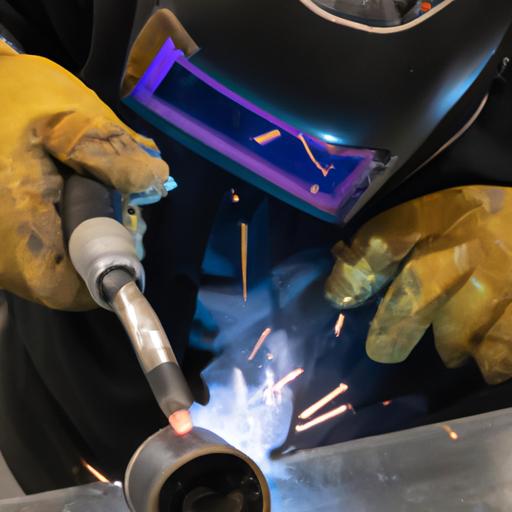
In the world of welding, two popular techniques stand out: MIG (Metal Inert Gas) welding and TIG (Tungsten Inert Gas) welding. If you’re new to welding or simply curious about the differences between these two methods, you’ve come to the right place. Understanding the dissimilarities between MIG and TIG welders is crucial for selecting the right tool for your welding projects.
Importance of Understanding the Difference
Before we dive into the specifics, let’s take a moment to appreciate the significance of comprehending the dissimilarities between MIG and TIG welders. Imagine walking into a hardware store, ready to purchase a welding machine, but having no idea which one suits your needs. It can be overwhelming, right? By understanding the variances between MIG and TIG welding techniques, you can make an informed decision and avoid purchasing the wrong tool.
Brief Overview of MIG and TIG Welding Techniques
MIG welding, also known as Gas Metal Arc Welding (GMAW), is a welding process that utilizes a continuously fed wire electrode and a shielding gas to create an electric arc. This arc generates heat, melting the base metal and the wire electrode, which then fuse together to form the weld. MIG welding is known for its versatility, speed, and ease of use, making it a popular choice for both beginners and professionals.
On the other hand, TIG welding, or Gas Tungsten Arc Welding (GTAW), involves using a non-consumable tungsten electrode to produce the weld. The welder manually feeds a filler metal into the weld area, while an inert gas shield protects the weld from atmospheric contaminants. TIG welding offers exceptional precision and control, making it ideal for welding exotic metals, thin materials, and critical welds.
Now that we have a basic understanding of MIG and TIG welding techniques, let’s explore their differences in more detail. Stay tuned for the upcoming sections, where we’ll compare the equipment and setup, welding processes, material suitability, skill requirements, and cost considerations of MIG and TIG welders.
MIG Welding
A. Definition and Explanation of MIG Welding
MIG welding, also known as Gas Metal Arc Welding (GMAW), is a welding technique that utilizes a continuous wire electrode and a shielding gas to create an electric arc. The wire electrode, which serves as both the filler material and the electrode, is continuously fed through the welding gun. As the wire electrode melts, it fuses with the base metal, creating a strong weld joint.
MIG welding is highly versatile and suitable for a wide range of materials, including stainless steel, carbon steel, aluminum, and various alloys. It is commonly used in automotive, construction, and manufacturing industries. The process can be easily automated or performed manually, making it a popular choice for both beginners and experienced welders.
B. Advantages and Disadvantages of MIG Welding
Advantages:
- Speed and Efficiency: MIG welding allows for fast and efficient welding due to the continuous wire feed.
- Ease of Use: This technique is relatively easy to learn, making it suitable for beginners.
- Versatility: MIG welding can be used on various materials and thicknesses.
- High Deposition Rates: The continuous wire feed enables high deposition rates, reducing overall welding time.
Disadvantages:
- Limited Weld Aesthetic: MIG welding may produce a less visually appealing weld compared to other techniques.
- Not Suitable for Thin Materials: MIG welding is less ideal for welding thin materials, as it can lead to burn-through or warping.
- Requires Clean Surface: Proper surface preparation is crucial for effective MIG welding, as contaminants can affect the quality of the weld.
C. Applications and Uses of MIG Welding
MIG welding finds applications in various industries, including:
- Automotive: MIG welding is commonly used in the automotive industry for manufacturing car frames, exhaust systems, and body panels.
- Construction: It is utilized in the construction sector for welding structural steel, pipelines, and metal frameworks.
- Manufacturing: MIG welding plays a vital role in fabricating metal components, machinery, and equipment.
- DIY and Hobbyist Projects: Due to its ease of use, MIG welding is popular among DIY enthusiasts and hobbyists for projects such as metal artwork, sculptures, and repairs.
Stay tuned for the next section, where we will explore TIG welding and its unique characteristics.
TIG Welding
Definition and Explanation of TIG Welding
TIG welding, also known as Gas Tungsten Arc Welding (GTAW), is a welding technique that utilizes a non-consumable tungsten electrode to create the weld. The electrode produces an electric arc that heats the base metal, while a separate filler metal is manually fed into the weld area. To protect the weld from atmospheric contamination, an inert gas, such as argon or helium, is used as a shielding gas.
TIG welding excels in providing precise control and accuracy. The non-consumable tungsten electrode, resistant to high temperatures, ensures consistent performance and longevity. This welding method is renowned for producing clean and aesthetically pleasing welds with minimal spatter and distortion. Due to its versatility, TIG welding is suitable for a wide range of applications, including automotive, aerospace, and artistry.
Advantages and Disadvantages of TIG Welding
TIG welding offers several advantages that make it a preferred choice for many skilled welders. Firstly, the ability to weld various metals, including stainless steel, aluminum, and copper, makes TIG welding highly versatile. Additionally, the precise control over heat input and weld pool size allows for welding thinner materials without compromising strength.
Moreover, TIG welding produces high-quality welds with exceptional aesthetics. The absence of spatter and minimal cleanup reduce post-welding work significantly. TIG welds are known for their strength, durability, and resistance to corrosion. Furthermore, the ability to weld in all positions enhances the flexibility of TIG welding.
However, TIG welding also has its limitations. This method is relatively slow compared to other welding techniques, which may be a disadvantage when working on projects with tight deadlines. The skill level required for TIG welding is higher, demanding a steady hand, precise control, and good coordination between the welder’s hand and foot movements. Additionally, the equipment for TIG welding tends to be more expensive, making it less accessible for casual or hobbyist welders.
Applications and Uses of TIG Welding
TIG welding finds extensive applications in various industries. Its precise control and ability to weld thinner materials make it suitable for delicate projects, such as jewelry making, artwork, and sculptures. Additionally, TIG welding is commonly used in the aerospace industry for welding critical components, such as aircraft frames and engine parts. The automotive industry also benefits from TIG welding, particularly in the fabrication of exhaust systems and fuel tanks.
In the construction sector, TIG welding is employed for welding stainless steel and aluminum structures, ensuring durability and corrosion resistance. Furthermore, TIG welding is often utilized in the manufacturing of medical equipment, such as surgical instruments and implants, where precision and cleanliness are paramount.
Stay tuned for the next section, where we’ll compare MIG and TIG welders, exploring their differences in equipment, welding processes, material suitability, skill requirements, and cost considerations.
Comparison between MIG and TIG Welders
Equipment and Setup Differences
When it comes to equipment and setup, MIG and TIG welders have some notable distinctions. MIG welding machines typically consist of a power source, wire feeder, welding gun, and a shielding gas system. The setup is relatively straightforward, making it user-friendly, even for beginners. On the other hand, TIG welding machines consist of a power source, tungsten electrode holder, foot pedal or hand control, and a shielding gas system. The setup for TIG welding requires more precision and control, making it slightly more complex than MIG welding.
Welding Process Variations
The welding process itself differs between MIG and TIG techniques. MIG welding operates on a semi-automatic or automatic process, where the wire electrode continuously feeds into the welding gun. The welder only needs to focus on maneuvering the gun and maintaining a steady hand movement. In contrast, TIG welding is a manual process that requires the welder to control the welding gun and simultaneously feed the filler metal into the weld area. TIG welding demands a high level of skill and dexterity, as it involves precise control of the welding arc, filler metal, and heat input.
Types of Materials Suitable for Each Technique
Both MIG and TIG welding techniques offer versatility in terms of material suitability. MIG welding is commonly used for welding steel, stainless steel, and aluminum, making it suitable for a wide range of applications, including automotive repairs, fabrication, and construction. TIG welding, on the other hand, excels in welding exotic metals, such as titanium, magnesium, and copper alloys. It is also the preferred choice for thin materials and critical welds, where precise control and a clean weld are crucial.
Skill Requirements for MIG and TIG Welding
The skill requirements for MIG and TIG welding differ significantly. MIG welding is relatively easy to learn and master, making it an excellent choice for beginners. With proper training and practice, one can quickly become proficient in MIG welding. TIG welding, on the other hand, demands a higher level of skill and experience. It requires precise hand-eye coordination, control over the welding arc, and the ability to manipulate the filler metal effectively. TIG welding is often considered a more advanced welding technique that requires time and dedication to become proficient.
Cost and Accessibility Considerations
Cost and accessibility are essential factors to consider when choosing between MIG and TIG welders. MIG welding machines are generally more affordable and widely available, making them a popular choice for hobbyists, DIY enthusiasts, and small-scale projects. TIG welding machines, on the other hand, tend to be more expensive due to their advanced features and precision capabilities. Additionally, TIG welding requires additional equipment, such as a tungsten electrode and filler rods, which can further increase the overall cost.
In the next section, we will delve into the factors to consider when deciding between MIG and TIG welders, including project requirements, material thickness, weld quality, skill level, and budget constraints. Stay tuned to make an informed decision!
Factors to Consider When Choosing Between MIG and TIG Welders
When it comes to selecting between MIG and TIG welders, several factors should be taken into consideration. Each welding technique has its strengths and weaknesses, so let’s explore the key aspects that can guide your decision-making process.
A. Project Requirements
First and foremost, consider the specific requirements of your welding project. Are you working on a large-scale industrial project or a smaller DIY endeavor? MIG welding is well-suited for high-speed operations and thicker materials, making it an excellent choice for projects that require quick and efficient welding. On the other hand, TIG welding offers superior precision and control, making it ideal for delicate and intricate welding tasks.
B. Material Thickness and Type
The thickness and type of materials you plan to weld are important factors to consider. MIG welding is known for its versatility and ability to weld a wide range of materials, including stainless steel, aluminum, and mild steel. It is particularly effective for thicker materials, as it can provide deep penetration and strong welds. TIG welding, on the other hand, excels in welding thinner materials and is commonly used for exotic metals like titanium and magnesium.
C. Weld Quality and Appearance
Are you aiming for impeccable weld quality and a clean, aesthetically pleasing appearance? If so, TIG welding might be the preferred choice. TIG welds are renowned for their smooth finish, minimal spatter, and excellent control over the heat input. On the other hand, MIG welding might result in a slightly less visually appealing weld, but it offers faster welding speeds and is more forgiving when it comes to variations in technique.
D. Skill Level and Experience
Consider your skill level and experience as a welder. MIG welding is generally easier to learn and master, making it an excellent option for beginners or those who require a more straightforward welding process. TIG welding, on the other hand, requires a higher level of skill and dexterity, as it involves manually feeding the filler metal while controlling the heat and maintaining a stable arc.
E. Budget Constraints
Lastly, your budget plays a significant role in the decision-making process. MIG welders are generally more affordable, making them a popular choice for those on a tighter budget. On the other hand, TIG welders tend to be more expensive due to their advanced capabilities and precision. Consider your financial constraints and weigh them against the specific requirements of your projects.
By considering these factors – project requirements, material thickness and type, weld quality and appearance, skill level and experience, and budget constraints – you can make an informed decision and choose the welding technique that best suits your needs. Remember, there is no one-size-fits-all answer, as the choice between MIG and TIG welders ultimately depends on your specific circumstances and welding goals.
Conclusion
In conclusion, understanding the difference between MIG and TIG welders is essential for any welding enthusiast or professional. Both techniques have their unique advantages and disadvantages, and choosing the right one depends on various factors such as project requirements, material type and thickness, desired weld quality, skill level, and budget constraints.
MIG welding offers versatility, speed, and ease of use, making it suitable for a wide range of applications. It excels in welding thicker materials and is favored for its efficiency and productivity. On the other hand, TIG welding provides exceptional precision, control, and weld quality. It is commonly used for welding thinner materials, exotic metals, and critical welds that require utmost accuracy.
When deciding between MIG and TIG welders, consider the specific needs of your project. If you prioritize speed, efficiency, and versatility, MIG welding might be the right choice for you. However, if precision, control, and weld aesthetics are your primary concerns, TIG welding should be your go-to option.
Remember, investing in the right welder and technique can significantly impact the success and quality of your welding projects. Take the time to evaluate your requirements and skill level before making a decision. Whether you choose MIG or TIG welding, both techniques have their place in the welding world and can help you achieve impressive results.
In conclusion, don’t underestimate the importance of understanding the difference between MIG and TIG welders. By doing so, you’ll be equipped with the knowledge needed to make an informed decision and select the right welding technique for your specific needs. Happy welding!
Conclusion: So above is the What is the Difference Between MIG and TIG Welders? article. Hopefully with this article you can help you in life, always follow and read our good articles on the website: cook.mahjong-gratuit.net